
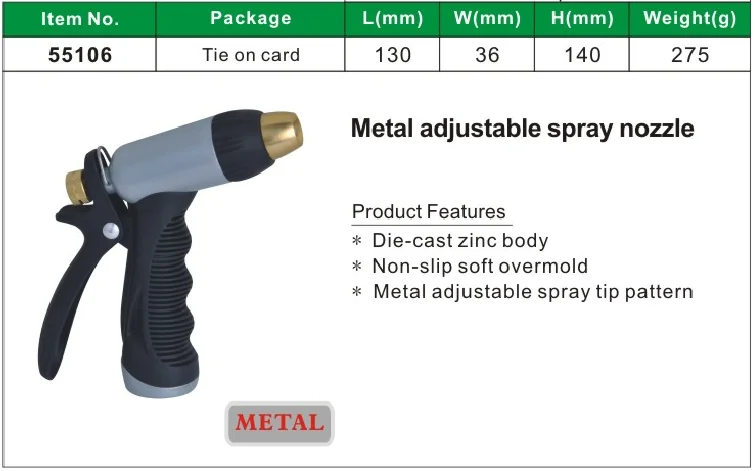
I simply used my copier to blow these views up to the size that I need. Based on the diameter of the fan blades, I figured that the fuselage should be about 40 inches from nose to tail. The model that I bought had these views in the painting instructions. Some of this is accomplished through artistic ability and some of it is cheating. I definitely need to start with a view from the top and a view from the side. It is essentially the same process as the construction for this projects plug.Īt this point, I can begin to produce profile drawings of the copter. It is not to build a mold however, it is geared toward building a hull and deck out of fiberglass. Yea, I have a simple build boat project that I am finishing now. I began to build the fuselage of the model and began to analyze the proportions, angles and curves of the copter. Using this model, I can get a good idea of the size that the fuselage has to be relative to the diameter of the fan blades in order to maintain a scale appearance. For this project, I selected a 1/35 scale UH-1. While 3D references are not always available, I do like to use them when possible. I use this model as a three dimensional reference. The first thing I like to do when I am building something like this is to go to the hobby store and pick up a model of the helicopter that I want to build. Of course the helicopter would have to be a classic – I chose the UH-1 from the Vietnam era. From the moment that I saw that fan, I thought that it would be cool to have a helicopter body that would hang from the underside of the ceiling fan making the fan blades look like rotor blades. I am sure that you have seen the fans that look like the nose of a WW II fighter plane. One project that I have wanted to do for a while was inspired by a ceiling fan that I first saw years ago. Typically, my projects involve building a plug, making a mold from that plug and finally using that mold to make pieces. I have made many things out of fiberglass over the years. That being said, this represents my initial post on this topic. The concepts of this project can be applied to ANY fiberglass molding project. The roving is guided by the boom crutch to make the roving smooth, less tangling, more uptime.I know that this is the boat forum but I am building a helicopter fuselage out of fiberglass and wanted to share the process with those who are interested. The whole system is mounted on a cart chassis which makes the equipment moveable, benefits the spraying flexible.Ĥ. Airless spraying decreases the volatilization and less pollution.ģ. Catalyst slave pump for exact catalyst ratio ensures the parts cured at desired rate.Ģ. The spray gun just needs to be cleaned few times, which greatly reduce the cleaning frequency and improve the production speed much.ġ.

Pump action, and mix together in the air. The resin and catalyst could be sprayed out respectively by the The fiber & resin spraying machine is multiple-use system for spraying resin and chopped roving synchronously. The price of the spray gun will be 6300USD based on FOB Ningbo port. The spray gun also can only use the resin. Using material: Calcium carbonate(CaCO3) powder, resin, solidifying chemical(catalyzer, catalyst)ĥ: Range of pecentage of solidifying chemical: 0.8_3%

The details of the spray gun for fiber glass and resin are as follows,
